Growth of silicon dioxide is performed using thermal oxidation, either in a dry or a wet ambient. For the highest quality oxides, such as gate oxides, dry oxidation is preferred (pure O2 ambient). Advantages are a slow oxidation rate, good control of the oxide thickness in thin oxides and high values of breakdown field. For thicker oxides, such as a field oxide in CMOS technology, wet oxidation is preferred (H2O ambient). The main advantage is a fast oxidation rate, so that a thick oxide (typically 0.5 µm) can be produced in a reasonable period of time (around an hour), thicker layers can be grown but at extended oxidation times. The main disadvantage of oxidation is that a high temperature is required of typically 900°C or above. For applications requiring a silicon dioxide layer produced at a lower temperature, plasma enhanced chemical vapour deposition can be used.
Oxidation Furnaces
For silicon 200 mm (8") dry and wet oxidation furnaces are available. These furnaces allow automated loading of up to 25 wafers in a quartz boat and provide oxidations at temperatures between 600 and 1150°C. Temperature accuracy can be controlled to better than ±1°C.
Jipelec Jetfirst 200/300
Where very thin silicon dioxide layers are required, rapid thermal oxidation can be used. Rapid thermal oxidation is a technique that provides a short (typically 30 seconds) oxidation at a high temperature using fast lamp heaters. Two Jipelec Jetfirst rapid thermal oxidation systems are available in the cleanroom, one for clean silicon processing and one for post-metal processing. Temperatures up to 1200°C can be reached and the oxidation time can be varied from 5 seconds to 10 minutes, with a ramp-up rate of 150°C/s. Absolute temperature can be controlled to within ±5°C. Temperature is generally measured using a thermocouple or a pyrometer depending on the process temperature requirements.
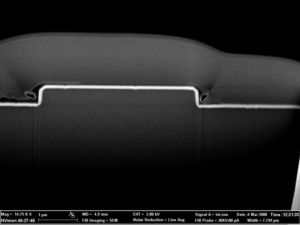