Wet etching provides a simple and cheap method of pattern transfer after photolithography. Its advantage is excellent selectivity (usually 100%), but its main disadvantage is that it gives little control over the etch profile. This means that wet etched windows tend to be bigger than their as-drawn size and wet etched lines tend to be smaller. If good control of window size or linewidth is required, dry etching can be used, which allows the etch profile to be varied from anisotropic to isotropic. Wet etches, such as the Secco, Sirtl or Wright etches (Journal of the Electrochemical Society, vol 124, No. 5, p757, 1977) can also be used for delineating crystallographic defects in silicon.
Wet Etch Room
The wet etch room provides a safe environment for wet etching of a wide variety of materials. The standard wet etch processes are given below.
Wet Etch | Comments |
7:1 buffered hydrofluoric acid | Thermal oxide etch, rate 100nm/min |
20:1 buffered hydrofluoric acid | Thermal oxide etch, rate 100nm/min |
Orthophosphoric acid @ 160C | Silicon nitride etch, rate 160nm/hr |
Orthophosphoric acid @ 37C | Aluminium etch, rate 0.1um/min |
Potassium hydroxide @ 70C | Silicon anisotropic etch, rate 0.7um/min |
KOH:H2O:methanol | Polysilicon etch |
HF:HNO3:H2O | Polysilicon etch |
RCA clean | Wafer clean |
Fuming nitric acid | Resist strip and wafer clean |
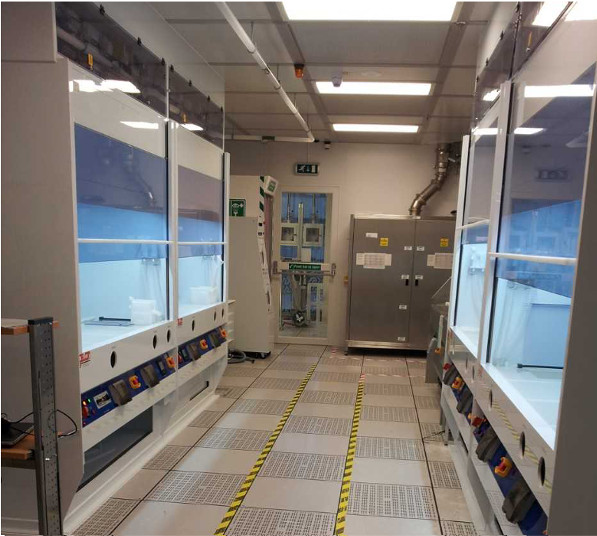