High temperature annealing is needed for a number of applications, including the repair of implantation damage, the densification of deposited insulators, the diffusion of dopants, for silicide formation etc. Anneals are usually done at a high temperature (900°C or above) and in a nitrogen ambient. However, if a completely inert anneal is required, anneals can also be performed in an argon ambient. The most common anneal method uses a furnace at a high temperature and an anneal time of typically one hour. However, shorter anneals are often required to minimise dopant diffusion and in this case a rapid thermal annealer can be used.
Tempress Anneal Furnaces
For silicon and other FEOL processes, several anneal furnaces are available for wafer sizes up to 200 mm (8"). These furnaces allow automated loading of up to 25 wafers in a quartz boat and provide oxidations and annealing at temperatures between 200 and 1050°C. Temperature accuracy can be controlled to better than ±1°C. For alloying of metal contacts, a low temperature anneal furnace is available which uses forming gas (a mixture of hydrogen and nitrogen). An alloy anneal is typically performed at 420°C for about 15 minutes and has the dual functions of providing a low resistance ohmic contact and of hydrogen passivation of the interface between silicon dioxide and silicon.
Jipelec Jetfirst 200/300 Rapid Thermal Annealers
Where very thin silicon dioxide layers or short anneal times are required, rapid thermal annealing can be used. Rapid thermal oxidation is a technique that provides a short (typically 30 seconds) anneal at a high temperature using fast lamp heaters. Jipelec Jetfirst 200 and Jipelec Jetfirst 200 rapid thermal annealers are available in the clean room, one for FEOL silicon/germanium processing and one for post-metal processing. Temperatures up to 1200C can be reached and the anneal time can be varied from 5 seconds to 10 minutes, with a ramp-up rate of up to 150°C/s. Absolute temperature can be controlled to within ±5°C. Temperature is measured using a thermocouple or a pyrometer depending on the temperature requirements of the process.
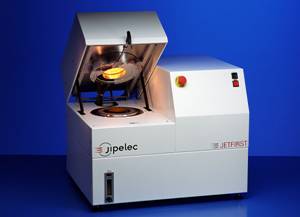